殼管式換熱器銅管縫隙腐蝕失效的分析
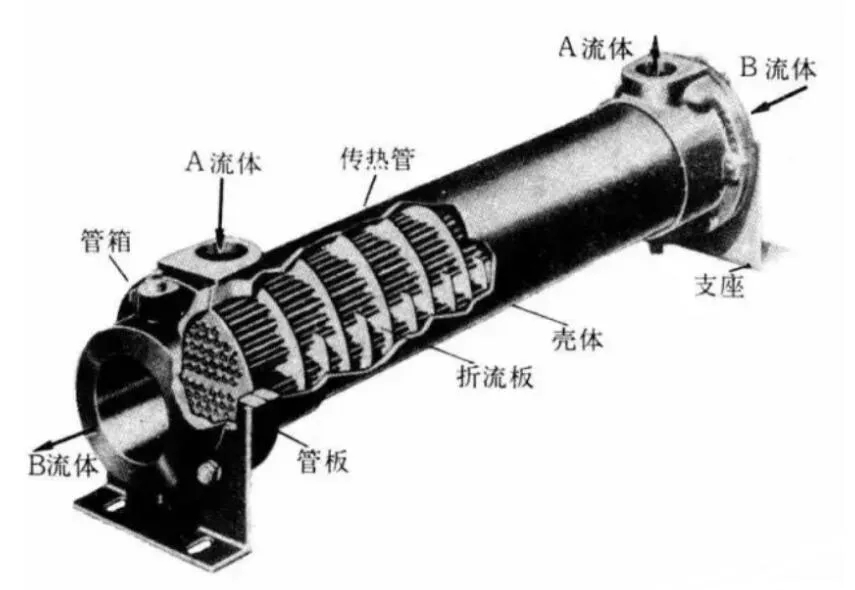
殼管式換熱器(圖1)由殼體、內(nèi)螺紋換熱銅管、折流板等部件組成。冷媒從1(冷媒進口)進入,流經(jīng)6(高效換熱銅管束)管內(nèi)換熱后從3(冷媒出口)流出,構(gòu)成管程。水從2-2(進水口)進入5(殼體),在6(高效換熱銅管束)外表面吸收熱量被加熱后從2(出水口)流出,構(gòu)成殼程。正常情況管程、殼程之間密閉、只有熱量交換不會發(fā)生流程材料泄漏。

出現(xiàn)失效的多臺商用空氣能熱水機殼管式換熱器在售后工作3.5年~5年后,先后反饋機組報“低壓保護”異常,維修人員排查確認為殼程流體(經(jīng)處理的地下水)已泄漏進入管程(圖2)。拆解發(fā)現(xiàn)折流板通孔處換熱管束銅材有不同程度腐蝕、穿孔(圖3銅管表面標紅處),出現(xiàn)位置在系統(tǒng)過熱、冷凝和過冷段未見明顯集中,可排除系統(tǒng)工作環(huán)境的溫度影響。
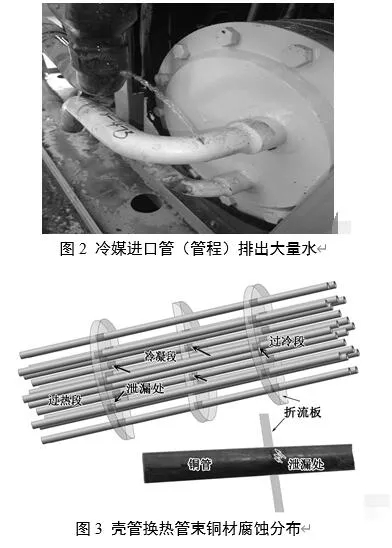
1.1 化學(xué)成分分析
對失效銅管取樣進行化學(xué)成分分析,結(jié)果(質(zhì)量分數(shù))與GB/T 5231要求相符。
1.2 力學(xué)性能試驗
在失效銅管上取樣進行力學(xué)性能檢測,結(jié)果與GB/T 17791要求相符。
1.3 斷口金相(OM)檢驗
將失效銅管外觀腐蝕深坑位做切面,并鑲嵌、研磨、拋光,使用三氯化鐵鹽酸溶液對試樣浸蝕,在金相顯微鏡下做斷口金相檢驗。
銅管外壁呈不規(guī)則蝕坑(圖4箭頭),內(nèi)側(cè)齒形完好未見明顯腐蝕,可以確定腐蝕方向為由外及內(nèi),及銅管表面或外側(cè)殼層水中含有相關(guān)腐蝕介質(zhì)。銅管基體為單相α銅(圖5),呈完全退火態(tài),晶粒平均直徑約為0.025 mm,最大凹坑底部仍有小的腐蝕坑貫穿造成泄漏。
1.4 掃描電鏡分析
將腐蝕泄漏銅管經(jīng)超聲波清洗后,置于PH ILIPS XL-30型掃描電子顯微鏡下觀察,圖6是泄漏處表面微觀形態(tài)。
可見,泄漏處內(nèi)表面存在腐蝕坑、裂紋、大量析出物,晶間優(yōu)先腐蝕形成深邃裂紋。對內(nèi)壁析出物(圖6譜圖1位置)進行X射線能譜分析(EDS),結(jié)果見圖7。
結(jié)果分析:在Cu基材正常元素限基礎(chǔ)上,F(xiàn)e、Al、Mg、Si、Cl等元素偏高原因可能來自工作環(huán)境的地下水質(zhì),其中元素Fe、Cl的含量嚴重超出水源水質(zhì)(見表1),為縫隙腐蝕反應(yīng)析出的產(chǎn)物。
1.5 水質(zhì)檢測
依據(jù)GB 29044《供曖水質(zhì)要求》標準與方法[9],對換熱銅管工作環(huán)境的補充水水質(zhì)進行取樣、測試,檢測結(jié)果如表1所示。
實驗測得含鐵量為18 mg/L,較GB 29044供暖水質(zhì)要求(總鐵≤1 mg/L)超過最大允許范圍17倍。
文獻指出,縫隙處于25~100 μm之間并且存在腐蝕介質(zhì),幾乎所有的金屬和合金都會發(fā)生縫隙腐蝕。本例殼管的銅管配入折流板通孔結(jié)構(gòu)的設(shè)計間隙在0.2 mm,實測配合間隙為0.02 mm~0.30 mm之間,水樣測試結(jié)果中Fe3+濃度18 mg/L(遠超于水質(zhì)標準要求的0.3 mg/L),同時存在一定量的Cl離子。組合形成的FeCl3通常用于工業(yè)上制印刷電路板時作為“腐蝕液”去除線路板上的多余銅,具有較強的腐蝕性,滿足縫隙腐蝕產(chǎn)生條件。具體過程Fe3+作用下金屬Cu在折流板縫隙或蝕孔中溶解,生成金屬離子Cu2+,造成縫隙或蝕孔中的正電荷過量,使Cl-遷移到縫隙或蝕孔中以維持其溶液的電中性,縫隙或蝕孔內(nèi)會存在高濃度的CuCl2,濃度梯度驅(qū)動CuCl2水解產(chǎn)生H+和Cl-,導(dǎo)致蝕孔進一步酸化、溶解(圖8)、直至局部穿孔,腐蝕反應(yīng)如下。
對殼管換熱管束銅材(含折流板)進行DOE試驗回歸分析,試圖尋找縫隙腐蝕速率、電位、電流與腐蝕介質(zhì)濃度、時間之間的關(guān)系。
2.1 實驗方法
取分析純氯化鐵與去離子水依次配置10 mg/L~140 mg/L不同濃度Fe3+(FeCl3)溶液,將換熱銅管束(含折流板)置于其中。實驗在熱水機工作溫度(90±5 ℃)條件下進行,每隔一段時間取出試樣檢查,并進行電化學(xué)參數(shù)實驗,直至銅材表面出現(xiàn)明顯腐蝕坑洞。
電化學(xué)參數(shù)實驗采用經(jīng)典的三電極體系,工作電極為銅電極,輔助電極為鉑電極,參比電極為飽和甘汞電極,使用PARSTAT2273電化學(xué)測量系統(tǒng)進行極化曲線測試:極化曲線掃描速率為0.5 mV/s,在實驗溫度下測試相對于SCE的腐蝕電位。
2.2 TAFEL曲線分析
熱銅管束(含折流板)在含不同濃度Fe3+溶液中浸泡216 h、432 h后銅材縫隙位的極化曲線如圖9。
從曲線圖可看出,換熱銅管的腐蝕受電荷轉(zhuǎn)移控制。采用PowerSuite軟件對極化曲線進行電化學(xué)等效擬合(表2)。
隨著氯化鐵的增加,Cu的腐蝕電位、腐蝕電流發(fā)生正移或增大,添加50 mg/L時的腐蝕電位正移幅度約為137 mV、腐蝕電流增大約113%(相對于10 mg/L),之后腐蝕電位的移動幅度較小、腐蝕電流明顯降低;金屬在介質(zhì)中的腐蝕電位與電流反映了金屬表面狀態(tài)和介質(zhì)特性。添加氯化鐵后腐蝕電流先增后減可能是由于Cu表面形成了某些暫態(tài)化合物或腐蝕產(chǎn)物阻礙腐蝕進一步進行。從表2中可以看出,腐蝕速率(腐蝕程度Icorr)隨著氯化鐵的增加呈現(xiàn)先增大后減小的趨勢,腐蝕在較低濃度下存在腐蝕峰值。
2.3 腐蝕試驗產(chǎn)物分析
將浸泡的換熱銅管取出并立即采用去離子水清洗,發(fā)現(xiàn)隔板位置表面呈現(xiàn)紫銅磚紅色和玫瑰紅色(圖11),金相分析發(fā)現(xiàn)腐蝕坑表面產(chǎn)生大量腐蝕產(chǎn)物,部分位置存在腐蝕產(chǎn)物覆蓋隔離現(xiàn)象(圖12)。
圖13為腐蝕產(chǎn)物能譜圖,銅表面腐蝕產(chǎn)物存在較高含量的C、O、Cu、Fe和Cl,其中O來自于腐蝕產(chǎn)物的吸附,表面該腐蝕產(chǎn)物部分位置較為疏松。較高含量的Fe表明氯化鐵中的Fe3+參與了反應(yīng)。對比圖7售后腐蝕產(chǎn)物明顯的Fe吸收峰,表明DOE試驗存在與售后反應(yīng)類似的腐蝕機理。
結(jié)論如下:
1)在10 mg/L~140 mg/L氯化鐵水溶液中,F(xiàn)e3+對Cu的縫隙腐蝕行為有重要影響,縫隙的濃度聚集作用在一定程度上促進了Cu縫隙腐蝕,高濃度時轉(zhuǎn)化為均勻腐蝕。
2)銅的縫隙腐蝕速率隨著Fe3+含量的增大呈現(xiàn)先增大后減少的趨勢,腐蝕產(chǎn)物對腐蝕有一定的阻隔作用。
3)考慮到熱水機殼管換熱器使用環(huán)境,高效換熱銅管的耐腐蝕性能優(yōu)秀,但在評估地下水等非標水質(zhì)對其腐蝕性影響時,應(yīng)將鐵離子含量控制考慮在內(nèi)。